REVIEWED P2 OPTIONS
| ||
Reviewed Oil and Gas - PBT Reduction OptionsFollowing are a list of options that have been reviewed by pollution prevention specialists. These options have worked at other facilities and may work at yours. |
||
Designate Waste Min. Employee | ||
Designating a specific person or position enhances waste minimization/pollution prevention prospects since at least one person becomes accountable to assess P2 opportunities and measure gains. | ||
Evaluate weight yield/volume yield | ||
Regular assessment of hydrocarbon loss is crucial to P2 efforts since a seemingly insignificant 0.01 % weight loss translates into approximately 40,000 - 50,000 lbs. hydrocarbon loss per month for a relatively small 50,000 BPD refinery. It is very difficult to reduce hydrocarbon losses to the environment if the refinery weight yield is not regularly completed to attempt quantification of the loss. | ||
Segregation of oily from non-oily wastes | ||
Segregation of these wastes significantly reduces total oily waste generation by avoiding contact of non-oily wastes with oily process sewers. Examples of non-oily process wastes to segregate from oily process wastewater systems include water softener sludges generated from lime softening for boiler water (& some cooling waters), boiler blowdown solids, etc. | ||
Control stormwater and windblown solids | ||
Successful, significant control of non-contaminated storm solids can avoid generation of hundreds of tons of oily waste by avoiding flow through oily wastewater system. These solids become coated with oil in process sewers and are subsequently deposited as waste in downstream separators, etc. Controls included fencing or covering of oily wastewater management structures (ex: ABTU's, equalization basins), curbing & paving earthen areas which could drain to oily wastewater system, sediment retention at oily sewer grates, re-routing stormwater, etc. | ||
Eliminate hazardous chemicals in the cooling tower | ||
Eliminate hazardous chemicals in the cooling towers. Examples of common chemicals include chromate corrosion inhibitors and pentachlorophenol biocides. Explore alternatives like conversion to phosphate corrosion inhibitors and to chlorine and or bromine-based biocides. | ||
Eliminate use of PCB's in electric transformers | ||
One way to do this is by: (1) draining Poly Chlorinated Biphenyls (PCB) dielectric oil from transformers; (2) adding non PCB oil; (3) placing transformer back in service for at least the TSCA regulatory requirement of 90 days and; (4) testing the dielectric oil for PCB content < 50 parts per million (ppm). IF necessary, repeat the process until the PCB content < 50 ppm. It may be better to change the whole transformer. Both initiatives reduce PCB pollution from future transformer leaks, accidents, etc. | ||
Eliminate use of mercury in instruments | ||
Removing instruments, storage tank vacuum "breakers" and other equipment containing mercury will significantly reduce the release of mercury into the environment from equipment leaks, accidents, fires and other mishaps. | ||
Maximize de-oiling/de-watering of oily wastes | ||
Results in significant P2 with recovery of hydrocarbons (HC) and avoids environmental costs of shipping water with wastes and saves energy with less water in wastes going to fuels programs, etc. | ||
Install oil/water interface probe in the crude oil | ||
Continuous level detection of oil-water interface with Agar probe significantly reduces oil losses to brine effluent of desalter unit and reduces corrosive contaminants in crude oil leading to downstream generation of hazardous wastes in fractionating towers, heat exchangers, etc. | ||
Add additional crude treating/ conditioning vessel | ||
Additional vessels installed upstream of crude oil desalter units will improve desalter performance with more gentle waterwash (avoiding tight emulsions), more residence time for sediment removal. This can result in less hazardous waste generation and hydrocarbon loss to brine wastewaters. Improved removal of sediments upstream of the desalter reduces plugging in the desalter brine draws consequently reducing concerns such as "vortexing," which leads to oil loss with brine wastewater. | ||
Mass flow meters in flare system | ||
Measuring flare gas flow rates is crucial step to reducing unnecessary hydrocarbon gas losses to refinery flare system. Mass flow measurements are often an innovative, significant improvement over volume flow measurements which are more vulnerable to erroneous fluctuations, corrosion, etc. | ||
Manufacture sodium hydrosulfide from spent caustic | ||
Recover spent caustic solutions and purify them to manufacture sodium hydrosulfide, a valuable component in metals refining & pharmaceutical production. | ||
Install oxygen analyzers installed in flue gas | ||
Significant energy savings can be achieved by controlling excess air/oxygen to furnaces. It eliminates the need to invest energy to preheat much more incoming air. | ||
Equip vacuum distillation unit eductors | ||
Eductors lower pressure in vacuum towers thereby lowering distillation temperature requirements. They also function to recover overhead vapors from distillation. Hydrocarbon loss can be significantly reduced with improved heat exchange system to condense vacuum tower overhead vapors. Fuel gas formerly lost can go to distillation unit furnaces and lower energy demands. | ||
Air cooler at Hydrodesulfurizer (HDS) unit | ||
Hazardous waste generated from conventional cooling water loop heat exchanger bundles can be avoided and energy conservation achieved by using air coolers/heat exchangers in place of cooling water. | ||
Modify Fluid Catalytic Cracking Unit | ||
Cyclone equipment used to separate fine catalyst particulates from Clarified Slurry Oils ("CSO" or heavy fuel oils) can be modified to significantly reduce source of listed hazardous waste. | ||
Pretreatment of storage tank water draws | ||
Put additional, modified oil/water/solids separator in place for storage tank field water draws. This significantly reduces oil contamination of wastewater and improves oil recovery. | ||
Gasification of wastes | ||
Wastes can be sent to gasification plant to produce clean, on-specification gas and liquid fuels instead of incineration. These include Clarified Slurry Oil (CSO) listed hazardous wastes, crude oil tank bottoms and other wastes. | ||
Improved heat exchanger control | ||
Add control equipment for more efficient routing of alkylation vent gas through Heat Exchangers (HETX) to reduce hydrofluoric Acid (HF) venting and improve overall gas (primarily propane) recovery at unit. | ||
Convert furnace burner to use ASO | ||
Recover BTU value of Acid Soluble Oil (ASO) instead of shipping it offsite as waste. | ||
Chloride guard beds | ||
Install adsorption beds to remove chlorides & other corrosive material in hydrogen-rich feed to compressor for distillate desulfurizer unit (DDU). This leads to reduced contaminants/waste and less compressor downtime. | ||
Improve slop oil recovery | ||
Add a tank mixer to improve efficiency of de-emulsifying agent in slop oil "rag layer"). This can result in less slop oil going to wastewater and/or hazardous waste. | ||
Segregate & recover spent caustic | ||
Different types of spent caustic can be segregated, collected and used for making cresylic acid instead of treatment and disposal. | ||
Upgrade crude oil desalter | ||
Upgrade desalter equipment to more efficiently remove salt and other impurities from crude oil. This can result in significantly reduced oil loss to wastewater and reduced generation of corrosion-derived hazardous waste in equipment downstream of the desalter (distillation/fractionating tower trays, overhead systems, etc.). |
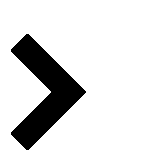